The Comprehensive Guide to Plastic Molding Electrical Solutions
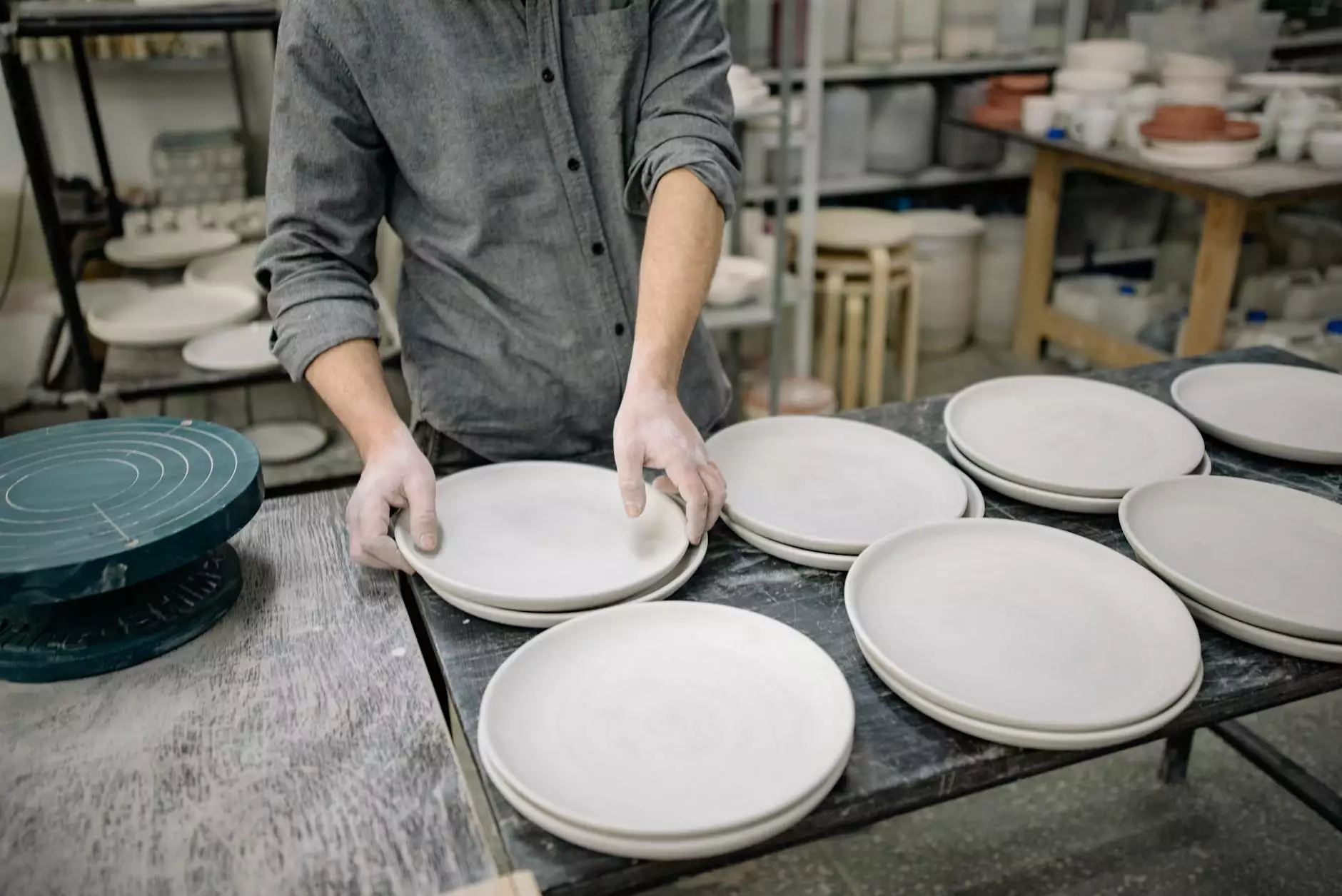
Understanding Plastic Molding Electrical
Plastic molding electrical is a vital aspect of modern manufacturing, bridging various industries from electronics to automotive to household products. This advanced process allows for the creation of intricate and durable components that meet the rising demands of quality, efficiency, and cost-effectiveness. At Deep Mould, we specialize in delivering high-quality solutions that leverage the latest technologies in plastic molding electrical.
What is Plastic Molding Electrical?
Plastic molding electrical involves the process of shaping plastic through various techniques to create parts that are essential for electrical applications. This includes the production of items such as switches, connectors, and housings that are used in countless electronic devices. By utilizing a variety of molding techniques, manufacturers are able to produce complex geometries and ensure that each component meets stringent industry standards.
Key Techniques in Plastic Molding
The main techniques employed in the plastic molding electrical space include:
- Injection Molding: This method injects molten plastic into a mold to create precise and intricate shapes. It is particularly suitable for high-volume production.
- Blow Molding: Used primarily for hollow objects, this method allows for the creation of bags, containers, and bottles effectively.
- Rotational Molding: A process best for making large parts, it involves heating plastic in a mold that is rotated to distribute the material evenly.
- Compression Molding: In this technique, plastic is placed in a heated mold and pressure is applied to shape it, commonly used for rubber or thermosetting plastics.
The Applications of Plastic Molding in Electrical Engineering
The applications of plastic molding electrical are extensive and cover multiple areas:
- Consumer Electronics: Items such as mobile phones, laptops, and home appliances utilize molded plastic components for durability and aesthetics.
- Automotive Components: From dashboard panels to headlights, molded plastics are essential for vehicle performance and design.
- Medical Devices: Precision is crucial in the medical field, where molded plastics are used for syringes, kits, and other critical equipment.
- Telecommunication: Equipment such as routers and switches rely on molded plastic housing to protect internal components while maintaining functionality.
Advantages of Plastic Molding Electrical Solutions
The advantages of integrating plastic molding into electrical engineering are numerous:
- Cost-Effectiveness: Plastic molding reduces both material waste and production time, leading to significant cost savings.
- Design Flexibility: The process allows for complex designs that can be tailored to meet specific needs.
- Durability: Molded plastics often outperform traditional materials by providing resistance to impact, heat, and chemicals.
- Lightweight Nature: This quality contributes to efficiency especially in automotive and aerospace applications where weight reduction is crucial.
Quality Standards in Plastic Molding
At Deep Mould, we adhere to strict quality standards to ensure that all plastic molded electrical parts meet industry specifications. This is crucial in maintaining operational integrity and safety in applications that require high reliability. Regular audits, material inspections, and adherence to ISO certifications are some of the measures taken.
Deep Mould: Your Partner in Plastic Molding Electrical
With years of experience and a commitment to innovation, Deep Mould stands out as a leader in the field. Our advanced manufacturing capabilities enable us to produce high-quality electrical components that cater to various industries. We work closely with our clients to ensure that their specific requirements are met, from the initial design phase through to full-scale production.
Innovations in Plastic Molding Electrical
The field of plastic molding electrical is continuously evolving, with new technologies emerging that enhance production quality and efficiency. Innovations such as 3D printing and bio-based plastics are beginning to make their mark, allowing manufacturers like Deep Mould to adopt greener practices while improving design capabilities and reducing lead times.
Conclusion
In conclusion, plastic molding electrical is an indispensable process in the modern manufacturing landscape. As industries continue to seek cost-effective and innovative solutions, the demand for molded plastic components is set to grow. By choosing Deep Mould, you gain access to unparalleled expertise and quality in this crucial field. Join us as we shape the future of electrical manufacturing.
Contact Us
If you want to learn more about how Deep Mould can assist with your plastic molding electrical needs, feel free to contact us today!