Understanding Plastic Injection Mold Parts: A Comprehensive Guide
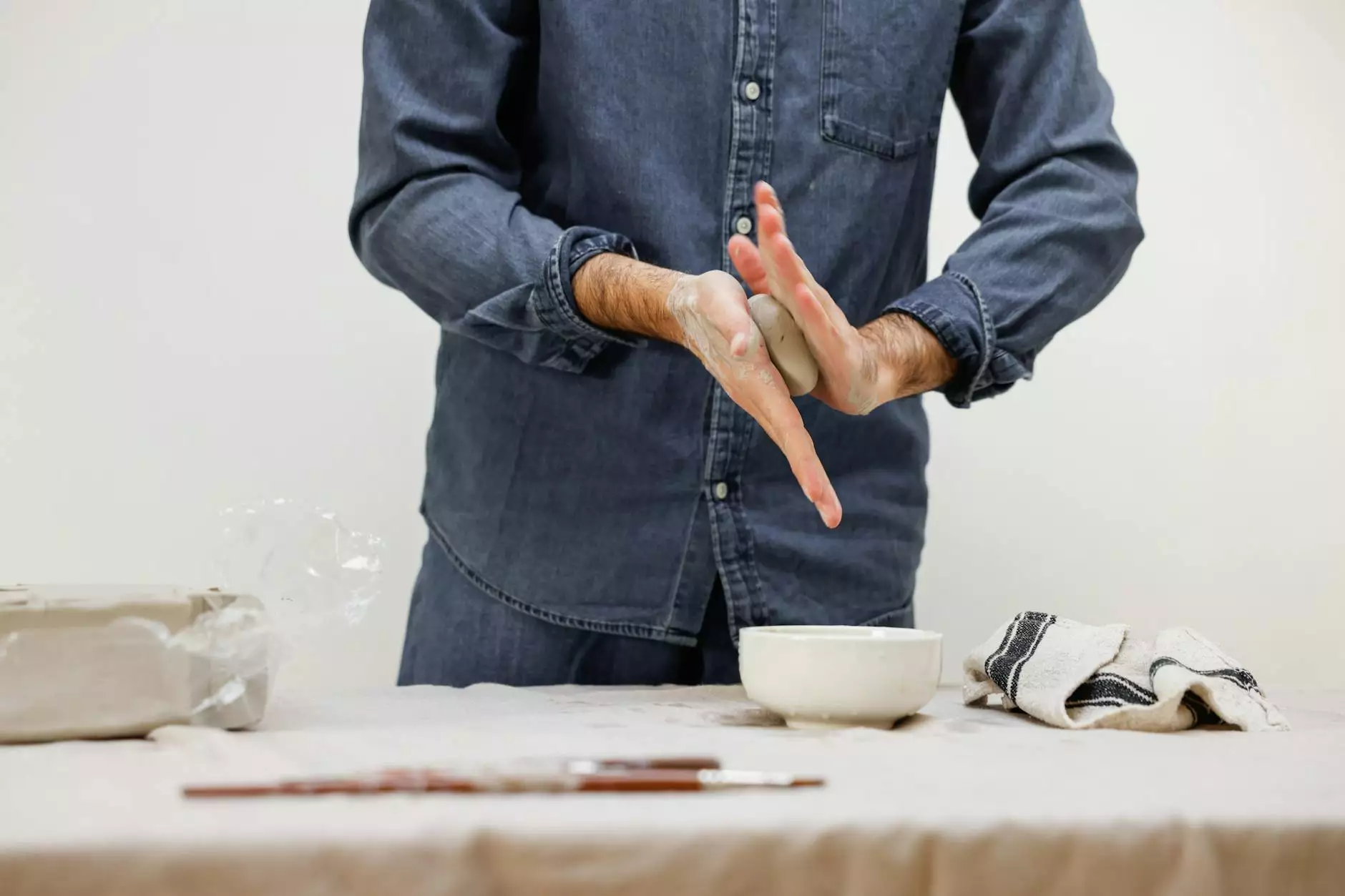
In the dynamic landscape of manufacturing, plastic injection mold parts play a pivotal role in ensuring efficiency, precision, and quality. As we delve deeper into the various aspects of these components, businesses can gain invaluable insights to enhance their operations. Whether you are a seasoned professional in the field of metal fabrication or a newcomer seeking to understand the industry, this guide is designed to provide you with comprehensive knowledge on this subject.
What Are Plastic Injection Mold Parts?
Plastic injection mold parts are components produced through a manufacturing process known as injection molding. This method involves injecting molten plastic into a mold, where it cools and solidifies to form a specific shape. The plastic injection mold parts are integral to various products across multiple sectors, including automotive, medical, consumer goods, and electronics.
How Does Plastic Injection Molding Work?
The process of producing plastic injection mold parts can be broken down into several key stages:
- Designing the Mold: The first step involves creating a detailed design of the mold using CAD software. This design must account for the part's dimensions, functionality, and the type of plastic to be used.
- Creating the Mold: After finalizing the design, manufacturers fabricate the mold, typically from steel or aluminum, depending on the production volume and complexity.
- Heating and Injecting Plastic: Once the mold is ready, plastic pellets are heated until they melt and then injected into the mold under high pressure.
- Cooling: The injected plastic cools and solidifies within the mold, forming the desired shape.
- Removing the Part: After cooling, the mold opens, and the finished plastic injection mold part is ejected.
The Importance of Quality in Plastic Injection Mold Parts
Quality is critical in the construction and performance of plastic injection mold parts. High-quality parts not only ensure that products function correctly but also enhance durability and longevity. Here are several reasons why focusing on quality matters:
- Performance: Quality parts work flawlessly, minimizing defects and enhancing product performance.
- Cost Efficiency: By reducing waste and preventing defects, high-quality molds save manufacturing costs in the long run.
- Reputation: Businesses that deliver quality products build a strong reputation, leading to increased customer loyalty and sales.
Applications of Plastic Injection Mold Parts
Plastic injection mold parts are remarkably versatile and find applications across numerous industries:
1. Automotive Industry
In the automotive sector, plastic injection mold parts are used in everything from interior components to exterior body panels. They help reduce the overall weight of vehicles, thereby improving fuel efficiency.
2. Medical Devices
Medical technology relies heavily on precise and reliable plastic mold parts. From surgical instruments to housings for diagnostic machines, quality assurance is paramount in this field.
3. Consumer Electronics
The consumer electronics industry benefits from injection molding for producing intricate parts that are both lightweight and durable, such as casings for phones, tablets, and other devices.
4. Household Items
Everyday household items, from kitchen utensils to furniture components, utilize plastic injection mold parts due to their affordability and vast design possibilities.
The Benefits of Using Plastic Injection Mold Parts
When businesses opt for plastic injection mold parts, they unlock a myriad of advantages:
- High Efficiency: The injection molding process allows for rapid production of parts, making it ideal for large-scale manufacturing.
- Complex Geometries: Injection molding can produce complex shapes that would be difficult or impossible to achieve with other manufacturing methods.
- Cost-Effective: Although the initial investment in molds can be high, the ability to produce large quantities effectively reduces cost per part.
- Material Versatility: A wide range of plastic materials can be used depending on the end product's requirements.
Choosing the Right Plastic Injection Mold Parts Manufacturer
When selecting a manufacturer for plastic injection mold parts, businesses must consider several critical factors:
1. Experience and Expertise
Look for a manufacturer with a proven track record in producing high-quality molds. Their experience can be indicative of their ability to meet your specific requirements.
2. Technology and Equipment
Modern manufacturing technology leads to better precision and productivity. Ensure that your chosen manufacturer uses state-of-the-art equipment.
3. Quality Standards
Quality assurance processes are vital. A manufacturer that follows stringent quality control measures will more likely produce parts that meet industry standards.
4. Customer Service
Effective communication and customer support are crucial for addressing any concerns during the manufacturing process. Choose a partner that prioritizes excellent service.
Future Trends in Plastic Injection Molding
The field of plastic injection molding is continually evolving. Here are some trends shaping its future:
1. Sustainability
With increasing environmental concerns, manufacturers are focusing on sustainable practices. This includes using biodegradable materials and developing processes that minimize waste.
2. Smart Manufacturing
The integration of Industry 4.0 technologies, such as IoT and AI, is making manufacturing smarter. By utilizing data analytics, manufacturers can optimize production processes and enhance efficiency.
3. Customization
As consumer demand for customized products grows, manufacturers are investing in technologies that allow for more personalized production of plastic injection mold parts.
Conclusion
Understanding plastic injection mold parts and their significant role in the manufacturing landscape can empower businesses to optimize their production processes and improve product quality. By choosing the right partners and staying ahead of industry trends, companies can harness the full potential of this vital manufacturing technology. For more information and to explore high-quality plastic injection solutions, visit deepmould.net.
In summary, the value of investing in top-notch plastic injection molding cannot be overstated. As industries continue to evolve, staying informed will position businesses for success in an increasingly competitive market.