Ultimate Guide to Using Etchant for Stainless Steel 304 in Metal Fabrication
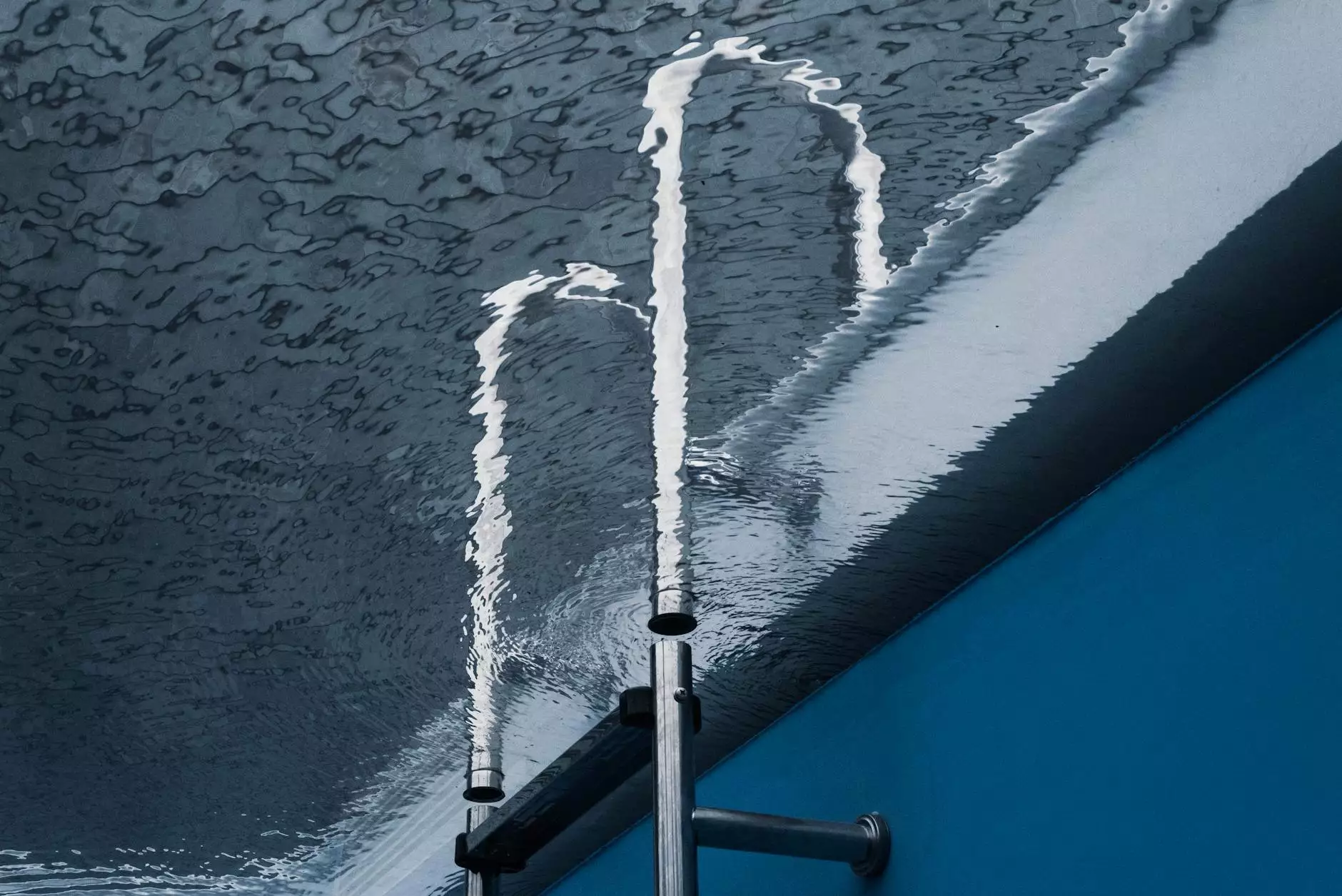
Introduction to Stainless Steel 304 in Modern Metal Fabrication
Stainless steel 304 is one of the most widely used grades of stainless steel, renowned for its exceptional corrosion resistance, excellent mechanical properties, and versatility across a multitude of industrial applications. Its chromium-nickel alloy composition makes it an ideal choice for environments exposed to moisture, chemicals, and high temperatures.
In the realm of metal fabrication, achieving the perfect surface finish for stainless steel 304 is essential for both aesthetic appeal and functional performance. This is where the use of an etchant for stainless steel 304 becomes integral, helping fabricators produce precise, high-quality finishes that meet rigorous industry standards.
Understanding the Role of Etchant in Stainless Steel Surface Treatment
An etchant for stainless steel 304 is a chemical solution used primarily to clean, passivate, or create decorative finishes on stainless steel surfaces. It acts by selectively removing surface impurities, oxides, and slight imperfections, thus enhancing corrosion resistance and providing an attractive appearance.
Beyond aesthetics, etching plays a crucial role in preparing the metal surface for further processes such as welding, coating, or sealing—ensuring optimal adhesion and longevity of the finished product.
Key Benefits of Using an Etchant for Stainless Steel 304
- Corrosion Resistance Enhancement: Proper etching removes surface contaminants and passive oxide layers, promoting a more consistent and protective oxide film formation.
- Improved Surface Quality: Achieves a clean, smooth surface which is ideal for application of paint, coating, or other finishing techniques.
- Decorative Finishes: Creates satin, matte, or brushed effects that appeal visually and improve tactile quality.
- Preparation for Fabrication: Facilitates better welding by reducing surface contaminants that could compromise joint integrity.
- Detection of Surface Flaws: Etching reveals cracks, pits, or other defects that could compromise structural integrity.
Types of Etchants Suitable for Stainless Steel 304
Various chemical compositions are employed as etchant for stainless steel 304, each suited for specific purposes:
- Chemical Pickling Solutions: These are typically acid-based solutions containing nitric and hydrofluoric acids, aimed at removing scale and rust.
- Passivation Solutions: Contain citric acid or nitric acid, designed to enhance the natural corrosion resistance by promoting formation of a passive oxide layer.
- Decorative Etchants: Typically mild acids or proprietary formulations, used for achieving aesthetic finishes and patterns.
Effective Usage of Etchant for Stainless Steel 304 in Fabrication Processes
Step 1: Surface Preparation
Before applying any etchant for stainless steel 304, thorough cleaning of the surface is vital. Remove grease, oil, dirt, and previous coatings using appropriate solvents or detergents. Mechanical methods like grinding or abrasive blasting may be employed to attain a uniform surface texture, which ensures the etchant’s effectiveness.
Step 2: Choosing the Right Etchant Solution
Select an etchant tailored for your specific project goals—whether it's cleaning, passivation, or decorative finishing. For industrial applications, choosing high-quality, industry-approved solutions from reputable suppliers like Goldeco Steel can significantly impact the outcome.
Step 3: Application Method
- Immersion: Submerging the stainless steel components in the etchant bath for controlled durations.
- Brushing or Wiping: For smaller parts or detailed work, applying the etchant with brushes or cloths ensures precision.
- Spraying: Using spray systems for large or complex surfaces allows uniform coverage and process control.
Step 4: Monitoring and Timing
Time management during etching is critical. Over-etching can lead to excessive material removal and surface roughness, while under-etching may leave contaminants behind. Regular inspection and adherence to manufacturer guidelines help optimize results.
Step 5: Rinsing and Passivation
After the desired etching effect is achieved, thoroughly rinse the components with clean water to remove residual acids. Follow up with passivation treatments to stabilize the surface, enhancing corrosion resistance and prolonging device lifespan.
Safety Considerations When Handling Etchant for Stainless Steel 304
- Protective Equipment: Always wear gloves, goggles, and acid-resistant clothing.
- Ventilation: Conduct etching in well-ventilated areas or use fume extraction systems.
- Proper Storage: Store chemicals in clearly labeled, corrosion-resistant containers away from incompatible substances.
- Disposal: Follow local regulations for disposing of acid waste to prevent environmental contamination.
Innovations and Industry Trends in Etching Technologies
The landscape of etchant for stainless steel 304 is evolving with advancements in environmentally friendly solutions, nanotechnologies, and automated processing systems. Some notable trends include:
- Eco-friendly Etchants: Development of less hazardous, biodegradable solutions that reduce ecological impact while maintaining efficacy.
- Laser Etching Enhancements: Combining chemical etching with laser techniques for intricate designs and high-precision finishes.
- Automated Processing: Integration of robotic systems for consistent, high-speed etching operations suitable for mass production.
- Surface Nanoscale Modification: Employing innovative etchants to alter surface properties at the nanoscale for specialized applications like biomedical implants or electronics.
Choosing the Right Partner for Metal Fabrication and Etchant Supplies: Goldeco Steel
As a leading metal fabricator specializing in stainless steel products, Goldeco Steel offers not only high-quality materials but also expert guidance on surface treatment processes, including the optimal use of etchant for stainless steel 304.
Our extensive experience allows us to assist clients from initial material selection to final finishing, ensuring all products meet exact specifications and industry standards. Partnering with Goldeco Steel means accessing the latest in chemical formulations, environmentally responsible practices, and innovative fabrication techniques tailored to your project needs.
Conclusion: Elevate Your Metal Fabrication with Proper Use of Etchant for Stainless Steel 304
Mastering the use of an etchant for stainless steel 304 is essential for producers aiming for premium surface quality, corrosion resistance, and aesthetic excellence. From careful surface preparation to choosing the right chemical solutions and applying best practices, every step in the process impacts the final outcome.
At Goldeco Steel, we emphasize the importance of quality materials, advanced technology, and expert knowledge to help our clients succeed. Whether you are creating decorative panels, industrial components, or precision-engineered assemblies, understanding and leveraging the power of proper etching techniques will ensure your projects stand out in the competitive marketplace.
Invest in precision, safety, and innovation—partner with Goldeco Steel today for the best in metal fabrication solutions.